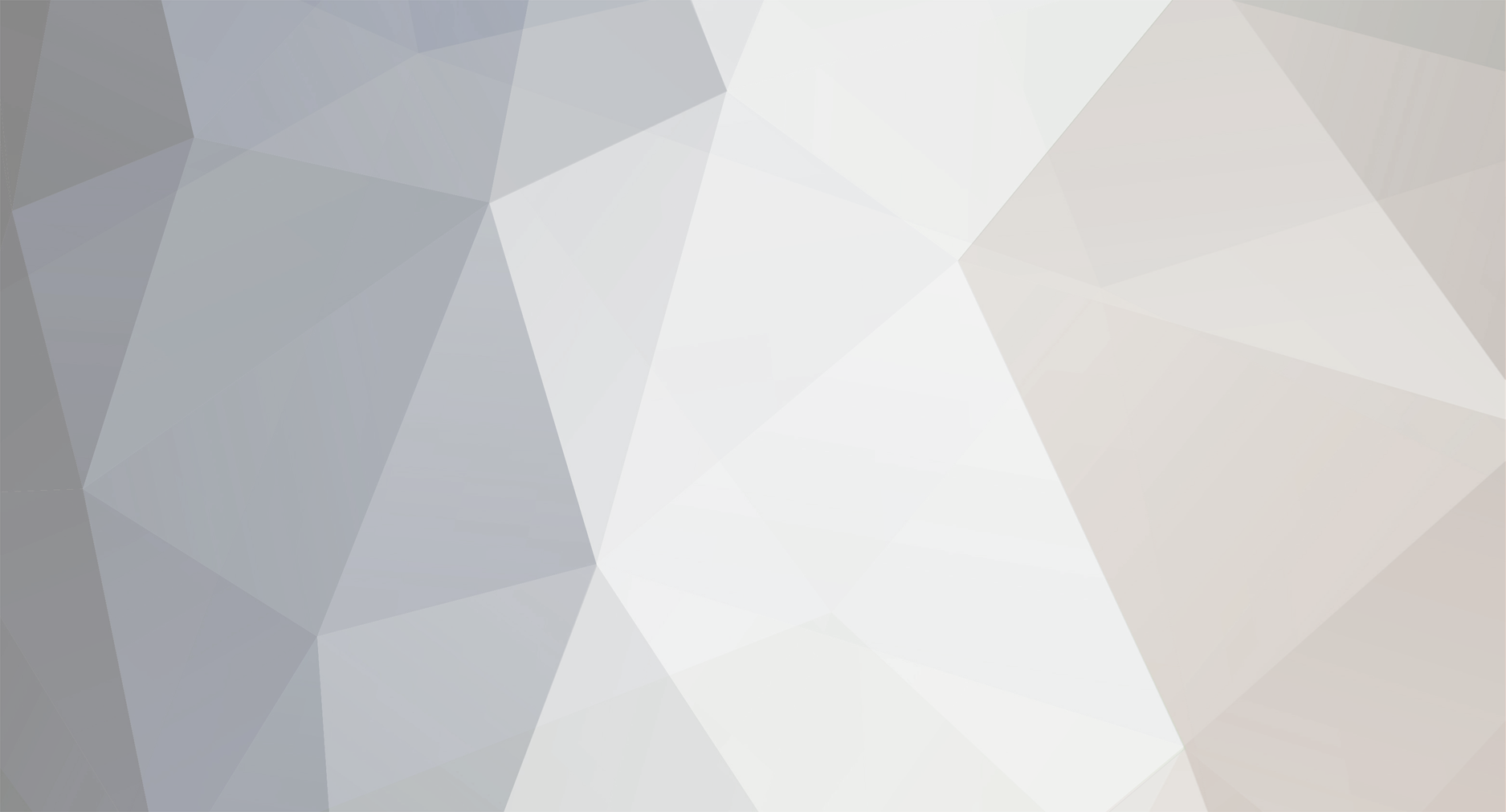
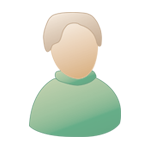
cuba
Участник-
Постов
12 -
Зарегистрирован
-
Посещение
Репутация
0 Обычный-
Параллельное включение
cuba ответил cuba тема в Силовая Преобразовательная Техника
Меня интересует не включение в параллель готовых источников, имеющих данную функцию, здесь всё понятно, а разработка своего модуля симметрирования токов, для источников имеющих датчик тока. Может кто-то сталкивался? -
Параллельное включение
cuba опубликовал тема в Силовая Преобразовательная Техника
Добрый день! Хотелось бы узнать о данной тематике не много больше, может кто обладает информацией (статьи, ссылки и др.) или сталкивался с данной проблемой на практике (методы, подводные камни и др.). Буду премного благодарен. Спасибо. -
Сколько стоит BGA-пайка и простая.
cuba ответил Lider тема в Пайка и монтаж
В целом ситуация с ценообразованием не простая. Т.к. разница между рекламным буклетом и коммерческим предложением очень ощутима. Многое зависит от раскрученности бренда, загруженности производства, стоимости расходных материалов, стоимости трафаретов, дополнительных услуг (электроконтроль, упаковка, рентгенографический контроль, различные "приёмки" и др.). Все эти моменты надо учитывать. Поэтому мой совет посчитать трудоёмкость по нормочасам и отдать всё это дело экономистам, они то знают как дальше считать. Больно дорого за корпус. Я делал не дороже 700 рублей с рентгенографическим контролем. Да и если честно все люди работающие в сфере контрактного производства прекрасно понимают, что при отработанном технологическом процессе установка чип компонента, QFP с 200 ногами или BGA ни чем не отличается. Но решающие слово в этом процессе это контроль качества паянного соединения. Хотя сейчас трудно об этом говорить так можно контролировать только форму и наличие пустот в выводе BGA компонента. Статистики о надежности таких паяных соединений полученных по комбинированной и бессвинцовой технологии пока нет в России. Поэтому рентгенографический контроль не панацея. -
Сдельная работа по пайке SMD-плат
cuba ответил korbnik тема в Предлагаю работу
Ваши координаты(где находитесь)? -
Контроль монтажа
cuba ответил wolfman тема в Пайка и монтаж
ФК — проверка изделия на соответствие ТУ + проверка на предмет выполнения штатных задач и функций. Давайте разбираться, в каких условиях работает ваше изделие (бытовая электроника, спец. техника, военная техника), т.к. существует 3 класса дефектов, то и подход различный, например один и тот же дефект может допускаться в бытовой и спец. технике, но не допустим в военной, или в принципе не допустим во всех трех классах изделий. Отсюда и контроль качества различный, и Ваше изделие например контрактное производство просто рассматривает как бытовое. Хотя если у Вас отваливаются компоненты, значит на лицо холодная пайка и не соблюдение технологии. Нам в этом случаи помогает микроскоп с 40х увеличением. Мы из 100 штук к примеру выбираем 10 и просматривает их. Руководствуемся стандартом IPC-А-610D «Критерии качества электронных сборок». Если визуально не определить дефект, хотя это бывает очень редко, то тут только испытания помогают(вибростенд, старение и т.д.). -
Контроль монтажа
cuba ответил wolfman тема в Пайка и монтаж
Пункт 4 Вы имеете ввиду контроль качества паяного соединения или функциональный контроль? В целом с Вами согласен, но все же без рентгенографического контроля при пайке BGA в некоторых случаях уже не обойтись. Да конечно запускайте испытания, после функциональный контроль, если не работает, отсылайте обратно, раз у них там такой "не хороший" отдел технического контроля :). -
Флюс ЛТИ-120.
cuba ответил kotofey тема в Пайка и монтаж
Без особых проблем должен помочь спиртобензин "Галоша", но надо пробовать все опытным путем. Про Zestron и Vigon, честно говоря, что касается струйной отмывки - у нас не пошло. Да и как показали наши изыскания в этой области нет панацеи. Еще раз повторюсь, все надо проверять и пробовать. Да есть вопросик, нет ли возможности использовать другой флюс, я понимаю 5-я приемка, но все же? -
паста
cuba ответил Mahim тема в Изготовление ПП - PCB manufacturing
А почему смешно, даже при средней загрузке контрактного производства (2-е 8 часовые смены) подсчет расходных материалов дает хорошую выгоду :). -
Да тут нет ничего сложного, на замену монтажному отверстию приходит контактная площадка, толщина трафарета 0.2мм, чтобы было достаточное количество паяльной пасты, так можно ставить DIP размером от 8 до 48X. Могу выслать Вам стандарт на почту, если хотите.
-
Просим прощения, не успел все просмотреть, поэтому ответил. Про DIP корпус - раздел 13.1 вроде в стандарте.
-
Стандарт IPC SM-782 говорит Нам, что DIP-корпуса можно устанавливать на контактные площадки, заместо монтажных отверстий. Только нужно обеспечить нормальное количество пасты. Второй способ - селективная пайка, но это возможно если только chip-компоненты отстоят от монтажного отверстия на 3 и более мм. Третье решение - сажать chip-элементы на специальный клей. Волной я бы не стал пробовать т.к. если на плате большое количество компонентов объемного монтажа, лучше сделать ре дизайн платы и перевести большинство элементов на SMT технологию или на слой TOP, если их малое количество(не более 15 chip-элементов).
-
Паяльная паста
cuba ответил Alexashka тема в Пайка и монтаж
Собственно я бы сделал так: Изготовил трафарет из обычной пластиковой бутылки или пластикового листа (сверлом в шахматном порядке просверлить отверстия для ног QFP) - это минут 30 работы затраты минимальны; Изготовил ракель из полиуретана или плексигласа(чтобы скос был под углом 60 или 45 градусов) - это так же 30 минут работы и затраты тоже минимальны; Совместил бы плату и трафарет, и нанес пасту методом трафаретной печати. Вот и все, максимум 1.5 часа работы уходит на изготовление трафарета, ракеля и палеты для совмещения платы, и трафарета и потом хоть партию в 300 штук собрать так можно.