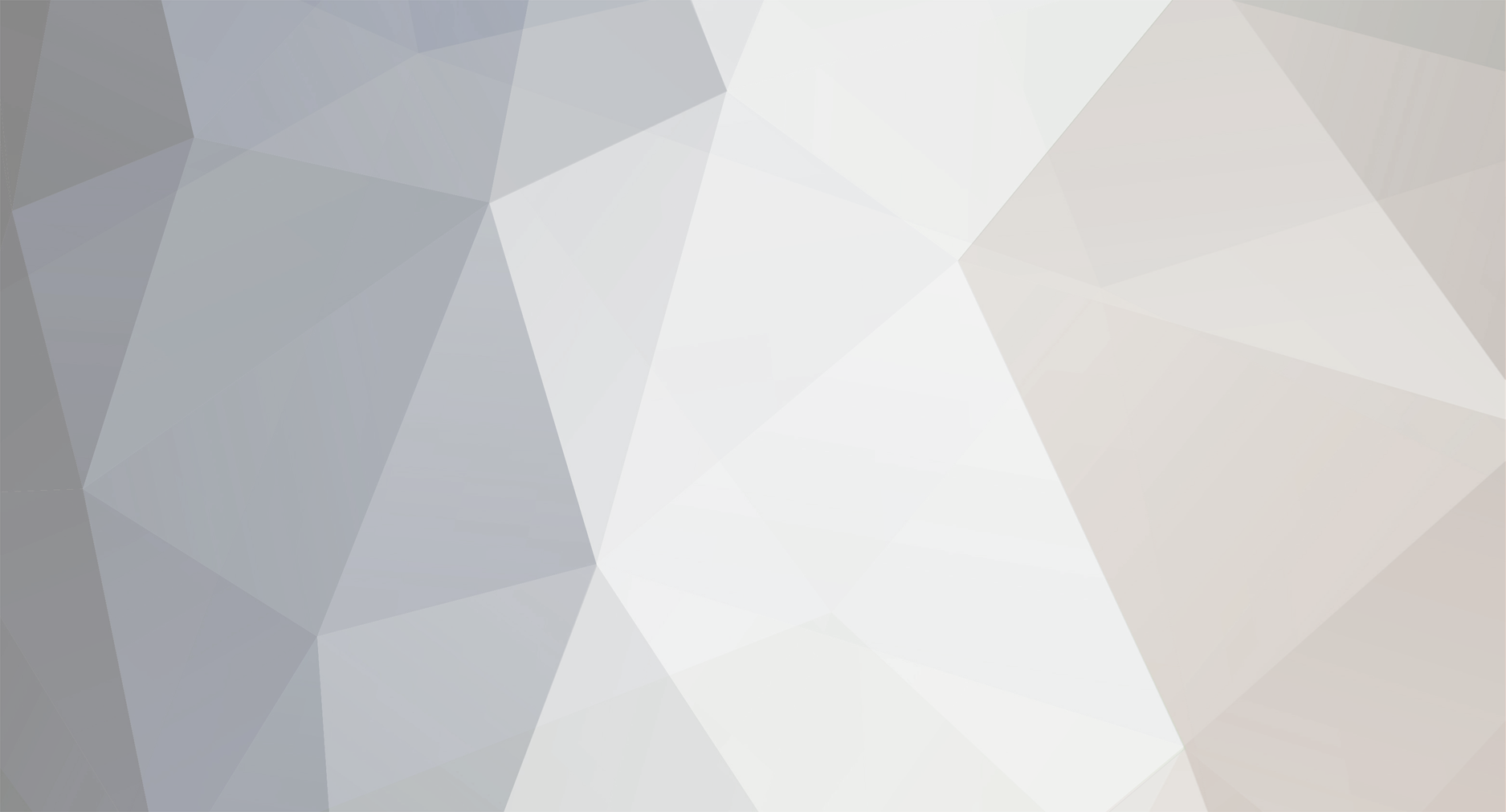
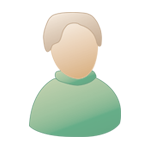
KESTVVV
-
Постов
61 -
Зарегистрирован
-
Посещение
Сообщения, опубликованные KESTVVV
-
-
7 hours ago, ZZmey said:
За счет чего?
Проще отмывать и как следствие трафарет испытывает меньше механических нагрузок.
-
Опубликовано · Изменено пользователем KESTVVV · Пожаловаться
2 hours ago, Атарасий said:Выбора как раз таки сегодня дофига. Паяльные роботы Quick начинаются от 400 тыр. Ruichi R351 (он же 1 Click Machine) немного дороже и приближается к 1 млн. Так что сегодня колхоз городить смысла мало.
QUICK 9334 скорее от 600тр . Если покупать за свой счет - то весьма немаленькая сумма.
Плюс как по мне эти цены вообще не оправданы. pnp станки куда сложнее изготовлены. -
10 minutes ago, Alt.F4 said:
А чем именно улучшают? Где-то натыкался, что при скруглении изменяются силы натяжения, сейчас никак не могу найти этот документ...
я стараюсь делать скругления побольше - так трафарет проживет больше. проще промывать. паста меньше застревает .
У прямоугольных падов не вижу никаких преимуществ. -
5 hours ago, Arlleex said:
Ну либо просто плотный трассировочный траффик. Острые углы сильно режут возможности под установленными Rules-ами.
Полностью согласен. Скругление улучшают пайку. А так же позволяют сделать более плотный монтаж .
-
3 hours ago, ENIAC said:
Первый минус эксплуатации - это то, что под каждый тип платы надо печатать индивидуальные оснастки, учитывающие все формы и высоты выводных компонентов. Этот вопрос решаемый, нужен опыт и 3Д-принтер. Второй минус - станок нормально так плюётся воздухом при очистке жала. Поставить поток меньше - не будет "стряхивать" избыток припоя нормально. Поставишь как надо - припой улетает с жала в разные стороны, в итоге - срач. Надо в конце смены вытирать, чтоб рабочее место имело какой-то вид. Третий минус (ну не то, чтобы минус, но место имеет быть): всё равно нужна подготовка компонентов - резка, формовка. Производительность растёт и вручную накусать и наформовать становится уже долго.
Моё мнение таково: для среднесерийного производства приемлемая штука. Для крупносерийсного - лучше селективная пайка. Для мелкосерийного лучше обычные монтажники. Ну и следить за состоянием жала надо постоянно, насколько оно уже прогорело. Идеально - выяснить его реальный ресурс и заменять его по графику, а не когда пошёл массовый брак. Это, кстати, касается и селективной пайки, даже несмотря на контроль высоты волны.
Сделать оснастку для каждой платы вообще не проблема. Эти роботы не для мелких серий. Для обрезки можно применять пневмокусачки. Опять таки - целесообразность заключается в стоимости ручного монтажа.Приветствую. сейчас как раз занимаюсь сборкой-разработкой 5 осевого паяльного робота.
Рама алюминий . Сложные узлы - напечатанные. Я понимаю что это типа кустарщина, но по сравнению с ручным монтажом, или покупкой готового станка за 2 млн - как то вари антов нет особо.
На счет "дальше картинок ничего не получится" - я собрал установщик на 95 питателей, и с паяльным роботом думаю все получится.(в соседней теме я его описывал )
Идея следующая - есть таблица координат сверловки, эту таблицу дополняем параметрами двух углов, времени пайки и количества припоя.
Сбоку есть еще ИК подогрев места пайки. Жало т12. -
-
Здравствуйте. Решил вот поделиться информацией о своем станке.
1 большое количество питателей обусловлено удобством монтажа различных плат в кратчайшие сроки и без перенастройки оборудования. Сейчас у нас в производстве находится порядка 10 различных приборов. На многие из них необходимо по 50-60 различных компонентов. Ставить два простых станка , и прогонять плату по очереди в каждый из них я не думаю что лучшая идея для не сильно массовых заказов 100-200 штук за раз. Все это приводит к необходимости большого количества разных питателей. И вот тут начинаются проблемы. "стандартные" питатели имеют ширину 11-15мм для 8мм ленты . На три стороны питатели не особо удобно ставить. Значит питатели с двух сторон. Для реализации сбалансированного сочетания различной ширины лент необходимо порядка 2 метров рабочей зоны пинцета. если на 2 стороны - то получается порядка одного метра на сторону. А с учетом мертвых зон в силу размеров головы, элементов механики и конструктива - получается ширина только рамы станка будет 1.4метра минимум. И это был бы несуразный монстр, который не смог бы как то транспортироваться.
Далее я решил сделать самые узкие автоматические автономные питатели из всех возможных. Поиски концепций питателей были долгие. Понял , что все наработки что есть у самодельщиков слишком широкие. Начал осваивать 3д моделирование и спустя большое количество различных вариантов пришел к текущей версии питателя.
Главное мое достижение - добавочная ширина питателя относительно ленты - 0.6мм . Лента центрируется двумя заточенными гвоздиками, это дает достаточно четкое удержание ленты. Основной упор я делал на долговечность - по этому никаких скользящих толкателей - только прямое попадание иглы в отверстие.
Все эти нюансы приводили к требованиям к протыкающе - толкательному устройству. Полет фантазии привел к появлению специального челнока с иглой. Челнок имеет 3 шаговых двигателя. Первый двигатель выбирает питатель, второй двигает саму ленту, третий - опускает/поднимает иглу. Сам челнок имеет свою плату управления, которая управляется по RS485.
2. То что питатели разделены на 2 стороны - подтолкнуло меня на разделение их на разную ширину лент. По одну сторону 65 питателей 8мм , по другую- 35широких 12,16,24мм . Желание делать сменные форсунки пинцетов - блажь и глупость по причине ограниченности лишь одним пинцетом. Серийные серьезные станки имеют минимум 4 пинцета. у меня в приборах минимум 70% элементов это компоненты на 8мм ленту. По этому я решил сделать фиксированные форсунки: для больших 506, для 1206 - 504 , 0805 - 503.
3. софт........ я из тех мамонтов, которые пишут на ассемблере. В итоге есть главный контроллер - mega640 который работает с компом, отправляет данные о перемещениях челнокам и голове, отправляет gкоды плате управления моторами xy . Кинематика станка используется COREXY, выбрал ее как наиболее точная и сильная на мой взгляд. моторами xy управляет плата для 3д принтера , так как на голове еще расположен экструдер для 3д печати. Все управление станком - при помощи команд отправляемых текстовой строке программы терминала ком порта. Отправка файла проекта на "печать" тоже осуществляется в программе терминале. все настройки софта и позиций питателей находятся в текстовом файле. Это кстати стало весьма удобным вариантом управления. Файл получаемый от программы для трассировки плат имеет текстовый формат, я лишь для каждого элемента добавляю номер питателя и номер пинцета. Больше никаких доработок таблицы не производится. Монтаж может производится до 30 плат за раз - это особо актуально для мелких плат. В тексте файла для печати указываются координаты для каждой платы.
Open PNP я не смог настроить на работу нестандартных питателей, да и как то не хотел все завязывать на камеры.
4 Помимо 95 ленточных питателей есть паллеты и отсеки для специализированных нестандартных компонентов. Настройка координат производится в ручную, при помощи двух мини вебкамер и двух лазерных модулей, которые светят красным крестом. Общий вес станка -40-50кг. Габариты 1200 650 750 - главное что в дверной проем влезает))
У меня на канале 6 видео с описанием станка и демонстрацией его работы.
https://www.youtube.com/channel/UC7xa9GGs4UEMGGBIOTX2vVA
ПС Извиняюсь за качество видео. -
тогда ставьте какой-нибудь степ-ап после конденсатора перед МК, он и 5В держать будет и конденсатор высосет почти полностью до 1.5-2В, соответственно ёмкость можно и поменьше взять.
там ещё размеры тоже от напряжения зависят :)
если сразу в Дж/м3 считать может и вообще наоборот оказаться что не очень большие вольты запасать выгоднее.
ну и у суперконденсаторов диапазоны напряжений обычно довольно ограничены.
Мне важна повышенная надежность. А у суперконденсаторов с этим похуже , чем у электролитов даже. Да и цена....
Как раз таки с высоким напряжением выгоднее запасать энергию.
-
А где у вас стоит диод и 10 т мкФ? Сразу за преобразователем, и там получается еще много чего висит на этих 5В? Вам предлагали поставить диод прямо перед МК, а за ним конденсатор, тогда кроме МК от него питаться никто не будет.
Я в начале уже указал , что 10 000 мкф идет только на питание контроллера через диод шоттки. А остальные цепи - запитываются напрямую от 5 вольт
-
Опубликовано · Изменено пользователем KESTVVV · Пожаловаться
Поставьте диод с конденсатором прямо перед контроллером, остальные нагрузки запитайте напрямую до диода. Емкость можно будет уменьшить на порядки и успеть сохраниться до критического снижения питания. По основному вопросу - я в такой же точно ситуации не стал полагаться на случай, сменил процессор с m8 на m88 (его работа при 2.7 В гарантируется до 10 МГц) и понизил рабочую частоту до 10 МГц.У этого прибора жесткие требования по быстродействию. На данный момент у меня как раз так и работает . Но я в итоге просчитался с величиной энергии в электролите. В итоге перед стабилизатором поставлю 2200мкф с диодом. Стабилизатор питается от 12 вольт. Это дает раза в 2 больше времени , чем с диодом и 10000мкф.
оффтоп: лично из моего опыта - m88 инвалид как со временем оказалось. ее лучше заменять на мега168. Одна из проблем , что я наблюдал - порча еепром даже при напряжении 4.6 вольт.это кстати указано в ерате.
-
Неужто в процессе работы нельзя сохраняться? "Не верю."
Ресурс EEPROM ограничен. Имеется энкодер , который часто меняет свое значение. Его нужно сохранять перед выключением.
-
Можно ожидать "сюрпризов" при повышенной\пониженной температуре.
А запасать энергию надо не на рельсе 5В, а до нее. Не забываем, что енергия конденсатора пропорциональна квадрату напряжения.
Проблема в том , что по 5 вольтам подключено большое количество разных нагрузок, И далеко не все можно перевести в малопотребляющий режим.
А делать два преобразователя энергии и вести 2 линии питания - не совсем удобно.
-
Atmega32a 16MHz
Ситуация следующая – при пропадании питания нужно сохранять данные в EEPROM. Имеется детектор пропадания напряжения питания перед импульсным стабилизатором на 5V.
Детектируется при помощи встроенного компаратора.
BODLEVEL – 2.7V . Питание 5V к контроллеру поступает через диод шотки. После диода стоит элетролит на 10000мкф запущенный через резистор 0.47 ом , чтобы не сгорел диод.
При пропадании питания запускается процесс сохранения данных. Сохраняется за 40мс.К концу записи в EEPROM напряжение на контроллере – 4 V.
Но в документации атмел указано что для 16MHz диапазон напряжений 4.5-5.5v .
Прибор работает далеко не в одном экземпляре . Недавно заметил такой вот момент.
И у меня вопрос – на сколько критично функционирование на сниженном напряжении при максимальной частоте кварца в течение непродолжительного времени?
Есть вопрос и относительно других моделей Atmega, с таким же вопросом.
-
Была у меня как то проблема - хотел сравнивать сигнал,использовал оба входа компаратора. Была проблема на напряжении 0-0.5v - выдавал неправильное значение. В итоге пришлось использовать внутреннее опорное напряжение.
-
В DIP-корпусе всего одно питание VCC. Наверное остальные две точки подачи питания уже разведены в корпусе?
А ведь и то верно............ как-то странно выходит. Кристалл ведь один и тот же. И если сравнить распиновки - то две дополнительные пары питания просто ни к чему не подключены.
ответ, как всегда, в даташите:PDIP Package:
1] The sum of all IOL, for all ports, should not exceed 200mA.
2] The sum of all IOL, for port A0 - A7, should not exceed 100mA.
3] The sum of all IOL, for ports B0 - B7,C0 - C7, D0 - D7 and XTAL2, should not exceed 100mA.
TQFP and QFN/MLF Package:
1] The sum of all IOL, for all ports, should not exceed 400mA.
2] The sum of all IOL, for ports A0 - A7, should not exceed 100mA.
3] The sum of all IOL, for ports B0 - B4, should not exceed 100mA.
4] The sum of all IOL, for ports B3 - B7, XTAL2, D0 - D2, should not exceed 100mA.
5] The sum of all IOL, for ports D3 - D7, should not exceed 100mA.
6] The sum of all IOL, for ports C0 - C7, should not exceed 100mA.
Спасибо за информацию. раньше как то на это не обращал внимания.
То есть если пиковая общая нагрузка всех портов вписывается в пределы для dip корпуса - то получается можно остальные пары не запитывать?
-
Просто плата это тонкий стеклотекстолит на основе алюминия. Значит буду извращаться с перемычками.
Спасибо за ответы.
-
Приветствую.
Имеется atmega32a.У этого микроконтроллера имеется 4 пары выводов питания.На каждой паре устанавливают по керамическому конденсатору 0.1uF . все земли соединяются вместе под контроллером.
Аналоговых измерений не будет. Частота работы 16МГц.
Вопрос так уж необходимо запитывать все входы питания, учитывая тот факт что внутри они соединяются?
Я всегда соединял, но в одном из проектов появилась некоторая сложность связанная с разводкой платы.
Есть ли у кого личный опыт или вменяемая информация по данному вопросу.
-
Еще есть http://www.maximintegrated.com/en/products...ts/DS28E05.html Она конечно более навороченая, но зато в корпусе SOT23 ее хрен на плате найдешь, затеряется среди транзисторов. Ее так и прятали- одна из ног микроконтроллера управляет транзисторным ключем и по совместительству- 1-wire шина для спятанного ид чип.
Интересная конечно вещица, но у нее проблемы с доступностью и ценой....
-
Спасибо за информацию по DS2401.
-
А есть ли какие-то существенные отличия DS2411 от DS1990 , не считая корпуса и вывода питания?
-
Идентификация приборов по радиоканалу. Необходимо хотя бы 10 битное число .
Запись в EEPROM - не самый технологичный вариант.
-
Здравствуйте.
Имеется группа приборов на основе AVR. И у каждого из них должен быть уникальный номер.
Поэтому вопрос в следующем - каким самым бюджетным способом реализовать уникальные номера приборов.
Пока что единственный вариант - таблетка ds1990 наглухо впаянная в плату.
В микроконтроллерах AVR на сколько я помню нет информации о внутреннем уникальном коде.
Есть ли у кого мысли по поводу более технологичного и дешевого варианта?
-
Если еще актуально kestacdc(собака)mail.ru
-
Если еще актуально напишите на [email protected] .
Паяльный робот
в Пайка и монтаж
Опубликовано · Пожаловаться
Я так понимаю , что для всех станков такого типа нужно делать специализированную оснастку для поддержки деталей.